基于Fluent的径向滑动轴承油膜特性的仿真分析
2017年07月19日
1. 引言
长期以来,利用求解雷诺方程的方法研究滑动轴承特性具有计算时间短的突出优点,然其求解过程中忽略了惯性项、油膜曲率等因素的影响。近年来,随着计算流体力学技术的发展和计算机性能的提高,在实验的基础上通过CFD建模分析的方法,可以更好地对油膜轴承动特性进行描述,完成实验难以实现的力场测试。本文以公司DQ11-100电机滑动轴承为原型,通过Proe创建油膜三维模型并利用Gambit划分网格建立有限元计算模型,利用CFD软件Fluent对动压径向轴承在稳态下的三维力场进行仿真分析。
2. 计算模型及网格划分
2.1 轴承物理模型的尺寸
轴承简化物理模型如图1所示,采用顶端供油,主轴顺时针转动。
轴瓦内孔直径D=100mm;轴瓦宽径比B/D=1;依照生产经验及相关公式,直径间隙h=0.2013mm,据滑动轴承流体动压润滑理论,解得偏心率ε=0.6013,油膜偏位角θ=49.95°。
其他参数:初定电机转速n=3000r/min;润滑油密度设定为895Kg/m3,同时据经验公式,润滑油动力粘度0.018Pa·s;考虑润滑油粘性生成热,取定润滑油比热容为1885J/(Kg·K),热传导系数为0.4W/(m·K)。
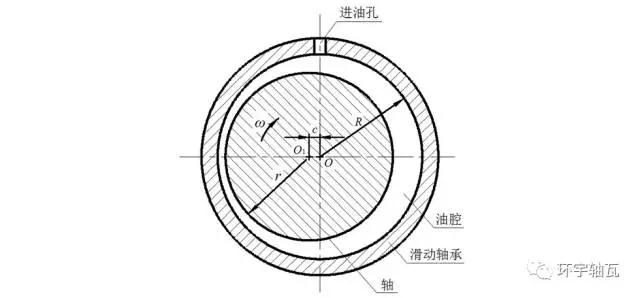
图1 滑动轴承轴向结构示意图
2.2 Fluent计算模型及网格划分
据上相关尺寸参数,于Proe中绘制滑动轴承油膜计算模型,考虑到轴承以及油膜润滑的对称性,为缩减计算时间,模型仅绘制一半,如图2a所示。
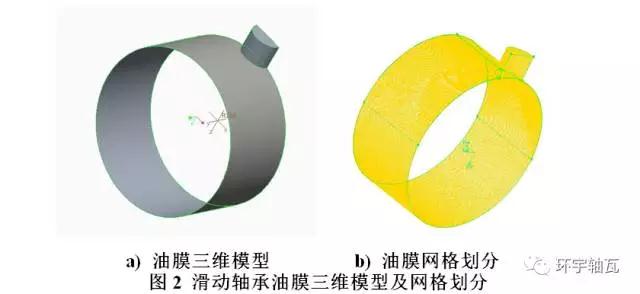
而后利用Gambit软件进行网格划分,为保证精度及后续求解计算的收敛,采用结构化网格,油膜厚度方向划分三层且等距分布,适当增加网格密度并作对称面处理,如图2b所示。
3. Fluent模拟仿真
3.1 多相流油膜计算条件的设置
模型的设定:采用压力基隐式求解器,三维的层流稳态模型,多相流模型使用混合模型Mixture,相数为两相。开启能量方程,在能量方程中包含粘性生成热ViscousHeating。
物相的设定:第一相为润滑油oil,其有效密度为895kg /m3,有效动力粘度为0.018Pa·s,比热容为1885J/(Kg·K),热传导系数为0.4W/(m·K)。第二相为空气air,其物性参数取自Fluent自带数据库。
边界条件的设定:选混合物为计算流体。进口压力设定为2000Pa,出口压力默认,设定主轴转速3000r/min,转速定义到油膜的壁面上。启用空穴模型,空气的初始体积分数0.1,油膜破裂压力为7550Pa,即当油膜压力低于7550Pa时,将析出空气。
3.2 计算结果
图3分别为偏心率ε=0.6013,转速n=3000r/min时的多相流油膜压力场、密度场、能量场以及温度场(开氏温度)分布。可见,
1) 油液从顶端进油孔流入,从轴瓦两端流出。油膜分布在最小油膜厚度附近呈现非常明显的压力集中区,顺着转轴旋转方向,压力从进油口逐渐增大达到正压峰值后减小,通过最小油膜厚度处后进入发散区,同时混合相密度逐渐减小,油膜在负压区迅速破裂,从而进一步影响了油膜的压力分布;
2) 在正压区,油膜温度较低,温升顺着润滑油流动方向从低温区向轴承两端扩张,同时随着轴颈转动方向,温度逐渐递增,且在油膜上半部分的负压区条带状区域内达到温升极限,继而由于低温润滑油从进油口的递补,温升又逐渐降低。
因而,通过压力分布和温度分布图可有针对性地改进轴承的散热结构,为轴承设计提供重要的理论依据,大大降低多次实验所需的高额成本。
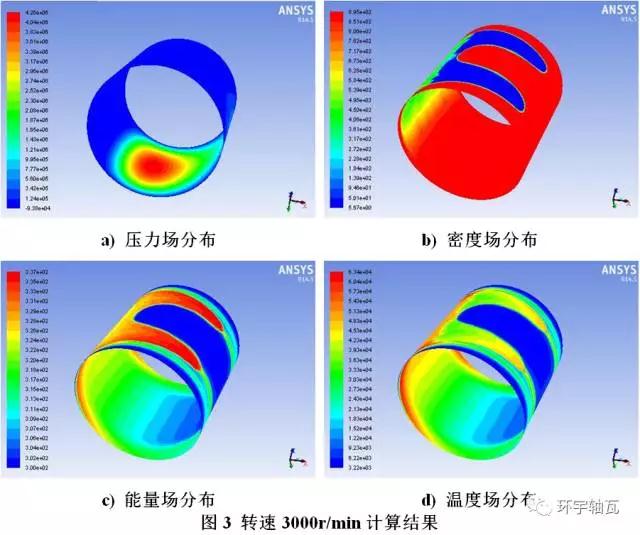
3.3 主轴转速对油膜特性的影响
改变主轴转速进行多次仿真计算,得到收敛后的稳态径向滑动轴承在转速分别为1000r/min、1500r/min、2000r/min、6000r/min时的压力场分布和温度场分布分别如图4、图5所示。
随着转速增大,油膜压力增大,油膜压力分布形态大致相同,周向油膜承载角度逐渐向最小膜厚位置方向收敛;且转速越大,温升越高,温升集中区越明显,轴向温度等值线向轴承中心位置收敛。
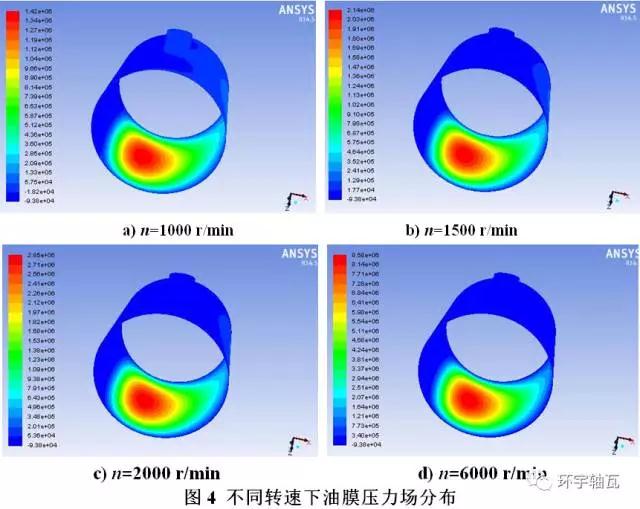
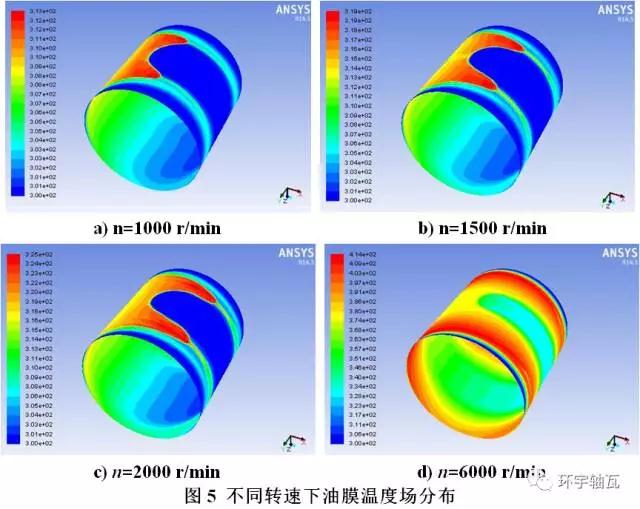
不同转速仿真实验中,轴瓦内孔100mm、宽径比为1,润滑油入口油温27℃,偏心率、直径间隙等参数为定值,设定不同的主轴转速,其计算结果数据如表1所示。据此可知,随着主轴转速增加,油膜压力极值及增大,温度极值及温升均显著升高,偏位角逐渐变小,轴心有下移趋势,油膜承载能力也随之增强。显然,主轴转速对油膜特性的影响规律与经典轴承理论相吻合。
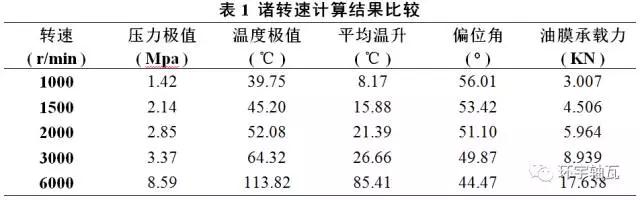
3.4 轴承参数的优化计算
如表1所示,转速为6000r/min时,压力极值极大,温度极值和温升已超出巴氏合金轴瓦的工作温度,因而此组条件参数不再适用。
重新计算轴瓦直径间隙和润滑油粘度,并进行油膜特性仿真实验,压力场分布及温度场分布如图6所示。具体仿真数据结果如表2所示,可见,压力极值和温度极值已大幅降低,理论上已满足实际使用条件。
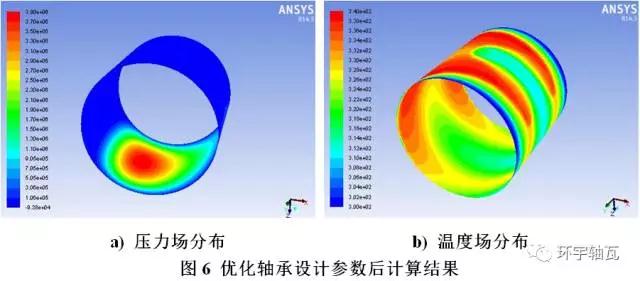
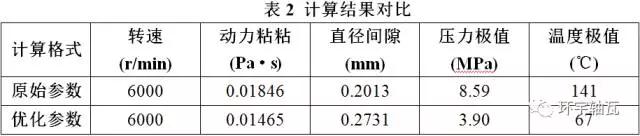
4. 结论
建立了基于Fluent的滑动轴承油膜计算分析模型,引入空穴模型以及粘温特性,给出流体流动压力场、温度场的时变分布情况,较为准确地反映滑动轴承轴承油膜稳态特性,预测流体在轴承中的流动状态和油膜的整体性能。工程设计与优化对实验的依赖性将大为减少,显著缩短设计周期,降低研发费用。
须强调指出,由于油膜计算模型本身的局限性,本文只对部分参数及计算数据做验证分析,但为实验的深入延续提供了较明晰的思路,为后续探索提供了有力的理论基础。
上一页:读解—巴氏合金的由来及特性
下一页:读解—汽轮机轴承简述